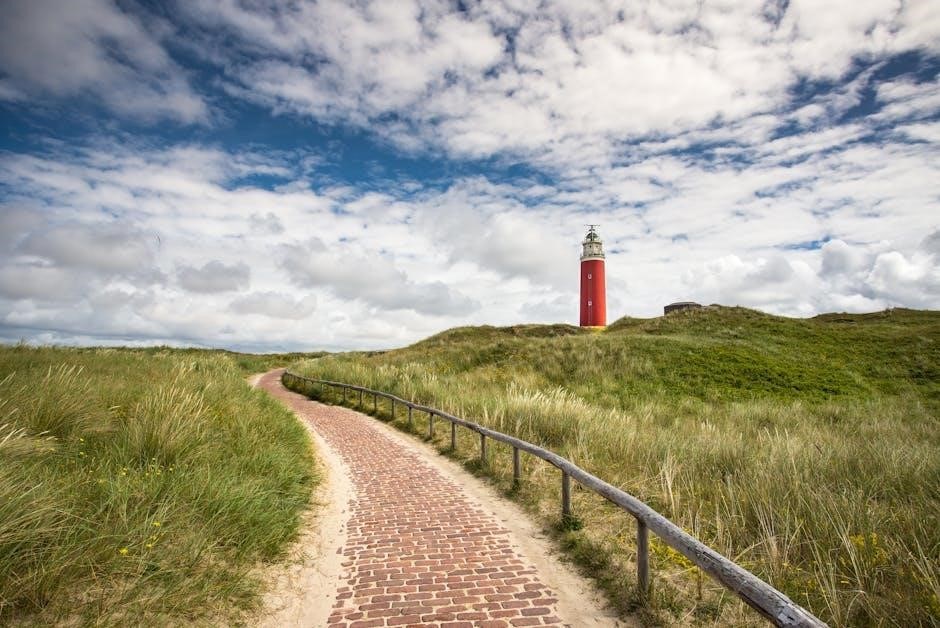
Slide and Guide Systems: An Overview
Slide and guide systems are crucial components in automated machinery․ They provide smooth, accurate linear motion, essential for various applications across industries․
Types of Slide and Guide Systems
Linear guides come in various types, each suited for specific applications and requirements․ Common types include ball type, sliding element, and track roller linear guides․
Ball Type Linear Guides
Ball type linear guides utilize circulating ball bearings positioned between the rail and bearing block, ensuring smooth and precise linear motion․ These guides are known for their high load capacity and ability to handle loads up to 38,000 Newtons․ Advantages include low friction, promoting efficient operation, and high stiffness, providing stability in demanding applications․ These guides support high moment loads, which can be up to 27․60 Newton meters․ The use of ball bearings minimizes friction, enabling high-speed movement and reducing wear․ Ball guides also offer exceptional precision, making them suitable for applications requiring accurate positioning․ Their robust design ensures reliability and longevity, even under heavy loads and continuous operation․ The compact size allows for integration into various machine designs․ Ball type linear guides are commonly found in machine tools, automation equipment, and other applications where precision and load capacity are essential․ They represent a versatile solution for linear motion requirements, balancing performance and durability in diverse settings․
Sliding Element Linear Guides
Sliding element linear guides feature a carriage or slide moving directly over a rail or guide surface, characterized by sliding contact․ Unlike ball-type guides, they lack rolling elements, resulting in uniform load distribution and high resistance, even under demanding conditions․ Sleeve bearing slides, a subset of this type, offer ease of operation and can manage loads applied from any direction․ However, they are less robust compared to dovetail and boxway slides, making them suitable for light to moderate load applications․ Simplicity linear slide assemblies use sliding contact between self-lubricating Frelon bearings and round rails․ One classic example is the dovetail slide, a straightforward linear-motion component․ These guides are well-suited for applications where simplicity and durability are paramount, and where the load requirements are not exceedingly high․ The absence of rolling elements contributes to their robust nature and resistance to contamination․ They are commonly used in applications requiring controlled, linear movement with moderate precision and load capacity․
Track Roller Linear Guides
Track roller linear guides utilize rollers that move along a track or rail to facilitate linear motion․ These guides often serve in challenging applications, including long-stroke linear-motion axes and linear systems in harsh environments․ Track-roller wheels can be customized through their internal bearing-element arrangements, sealing, and outer tread geometry and material makeup․ Variations in wheel geometries and their benefits are numerous․ Common designs employ thin cylindrical-shaped needle rollers for higher radial loads and speeds․ Cam followers with twin rows of standard ball-bearing elements are suitable for high loads․ Low Profile Redi-Rail is a low-profile track-roller option that employs Gothic arch wheels running on hardened steel races and can handle loads beyond 100 lb․ Track-roller linear guides are well-suited for applications requiring high load capacity and the ability to withstand demanding conditions․ They are frequently employed in material handling, automation, and other industrial settings where reliable linear motion is essential․
Components of Slide and Guide Systems
Slide and guide systems comprise several key components that work together to enable smooth and accurate linear motion․ The main components include the slide or carriage, the guide rail or track, and the bearing elements․ The slide or carriage is the moving part that supports the load and travels along the guide rail․ The guide rail provides a precise and stable pathway for the slide․ Bearing elements, such as balls, rollers, or sliding surfaces, reduce friction between the slide and the guide rail․ Other components may include wipers or scrapers to clean the surface of the rails and guides, ensuring smooth operation and preventing contamination․ End caps or seals may also be used to protect the bearing elements and prevent debris from entering the system․ The specific components used in a slide and guide system will vary depending on the type of system and the application requirements․ However, the core components of the slide, guide rail, and bearing elements are essential for providing reliable and accurate linear motion․
Applications of Slide and Guide Systems
Slide and guide systems are utilized across diverse applications, including material handling, factory automation, medical equipment, and machine tools, due to their precision․
Material Handling Machines
In material handling machines, slide and guide systems are integral for ensuring precise and reliable movement of goods and materials․ These systems facilitate the smooth operation of automated storage and retrieval systems (AS/RS), where accurate positioning is paramount for efficient inventory management and order fulfillment․ Linear guides, a key component of these systems, are employed in conveyor systems, robotic arms, and other material transfer mechanisms to maintain stability and minimize friction during movement․ The robustness of slide and guide systems, particularly those utilizing track rollers, enables them to withstand demanding conditions and heavy loads encountered in industrial settings․ Cross-roller ways or slide-way guides are also used to provide exceptional precision, smooth operation, and accuracy in applications requiring top performance․ This is essential in ensuring the safe and timely delivery of materials throughout the production process․ Furthermore, the adaptability of these systems allows for customization to specific machine requirements, optimizing performance and reducing downtime․ The use of linear slides in material handling also contributes to increased automation, leading to higher productivity and reduced labor costs․ Proper selection and integration of slide and guide systems are crucial for maximizing the efficiency and reliability of material handling operations․
Factory Automation
Slide and guide systems play a critical role in factory automation, providing precise linear motion for various automated processes․ These systems are essential for applications such as robotic assembly lines, CNC machines, and automated inspection systems, where accuracy and repeatability are paramount․ Linear slides and stages, incorporating linear bearings, minimize friction and guide movement, enhancing the efficiency and reliability of automated tasks․ Different types of linear guides, including ball-type, sliding element, and track roller guides, are chosen based on specific application requirements, such as load capacity, travel accuracy, and environmental conditions․ In robotic assembly lines, slide and guide systems facilitate the precise positioning of components, ensuring accurate and consistent assembly processes․ CNC machines utilize these systems to control the movement of cutting tools, enabling the creation of complex parts with high precision․ Automated inspection systems rely on linear guides to accurately position sensors and cameras, ensuring thorough and reliable quality control․ The use of cross-roller way or slide-way guides can further enhance precision and smooth operation in demanding applications․ By enabling precise and repeatable linear motion, slide and guide systems contribute to increased productivity, reduced downtime, and improved product quality in factory automation environments․ The selection of appropriate systems is crucial for optimizing performance and achieving the desired level of automation․
Medical Equipment
Slide and guide systems are indispensable in medical equipment, providing precise and reliable linear motion for a wide range of applications․ These systems are crucial for devices such as medical imaging equipment (e․g․, MRI, CT scanners), surgical robots, laboratory automation systems, and patient positioning systems․ In medical imaging, linear guides facilitate the accurate movement of imaging components, ensuring high-resolution and distortion-free images․ Surgical robots rely on these systems for precise and controlled movements of surgical instruments, enhancing surgical accuracy and minimizing invasiveness․ Laboratory automation systems utilize linear slides and guides to automate sample handling, dispensing, and analysis, improving efficiency and reducing the risk of human error․ Patient positioning systems employ linear guides to precisely position patients for treatment or diagnosis, ensuring optimal alignment and comfort․ Different types of linear guides, including ball-type, sliding element, and track roller guides, are selected based on specific requirements such as load capacity, travel accuracy, and cleanliness․ The use of materials compatible with medical environments, such as stainless steel and corrosion-resistant polymers, is essential to ensure hygiene and prevent contamination․ Furthermore, smooth and quiet operation is crucial to minimize patient discomfort and ensure accurate results․ By enabling precise and reliable linear motion, slide and guide systems contribute to improved diagnostic accuracy, enhanced surgical outcomes, and increased efficiency in medical procedures․ The selection and maintenance of appropriate systems are vital for ensuring the safety and effectiveness of medical equipment․
Advantages of Slide and Guide Systems
Slide and guide systems offer several key advantages, including high load capacity, exceptional travel accuracy, and superior rigidity, making them versatile․
Load Capacity
Load capacity is a critical advantage of slide and guide systems․ Different types of systems offer varying load capacities to suit specific application needs․ Ball-type guides, for example, can support high payloads, some reaching up to 38,000 Newtons (N)․ The capacity is influenced by the design and materials used, impacting both static and dynamic load ratings․ Real-world factors, like wear, environmental conditions, and maintenance practices, further influence the load-bearing capabilities over time․ Selecting the right system involves carefully considering the expected loads and operational conditions to ensure longevity and reliable performance․ Systems like roller bearings can deliver dynamic load ratings from 3,560 to 55,600 N․ It’s important to consult manufacturer specifications and consider safety factors in design calculations․ Furthermore, the mounting orientation significantly affects the load capacity, especially in vertical applications where gravity adds to the stress․ Proper alignment and support structures are also crucial for maximizing the load capacity and preventing premature failure of the slide and guide system․ The uniform load distribution across the sliding elements contributes to higher resistance, even under demanding operational conditions․
Travel Accuracy
Travel accuracy is a paramount advantage of slide and guide systems, particularly when exceptional precision is required for specific applications․ High-precision linear guides, such as cross-roller ways or slide-way guides, are often selected for their superior accuracy․ Factors affecting travel accuracy include the quality of the components, the precision of the manufacturing process, and the proper installation and alignment of the system․ Systems with recirculating rolling elements, like ball slides, offer consistent and repeatable motion, minimizing deviations along the travel path․ The use of wipers or scrapers to clean the surface of the rails/guides also contributes to maintaining accuracy by preventing debris accumulation․ Travel accuracy is also closely related to the rigidity of the system; higher rigidity reduces deflection under load, thereby improving accuracy․ Gothic arch designs have greater clearance and roller-to-rail contact that provides exceptional linear accuracy, but can make for lower load capacities․ The choice of lubrication also plays a role, as it reduces friction and ensures smooth, consistent movement․ Regular maintenance and inspection are crucial for preserving travel accuracy over time, as wear and tear can gradually degrade performance․ In applications where even slight inaccuracies can have significant consequences, careful selection and meticulous maintenance of the slide and guide system are essential․
Rigidity
Rigidity is a crucial advantage offered by slide and guide systems, particularly in applications demanding high precision and stability․ Linear rail guides, for example, excel in rigidity, enabling them to withstand loads from various directions, unlike round shaft guides that are limited to downward or liftoff loads․ This inherent stiffness minimizes deflection and deformation under load, ensuring consistent and accurate positioning․ The design and materials used in the construction of the slide and guide system significantly influence its rigidity․ Block slides, known for their rugged design, generally offer superior rigidity compared to other types․ The use of high-quality materials, such as hardened steel, further enhances the system’s ability to resist bending and twisting․ Furthermore, proper mounting and support structures are essential for maximizing rigidity․ Insufficient support can compromise the system’s overall stiffness, leading to inaccuracies and reduced performance․ Regular inspection and maintenance are necessary to maintain rigidity over time, as wear and tear can gradually degrade the system’s structural integrity․ Preloading rolling elements, such as balls or rollers, can also increase rigidity by reducing play and increasing contact stiffness․ In applications where vibrations or external forces are present, high rigidity is paramount for ensuring stable and reliable operation․ Ultimately, selecting a slide and guide system with adequate rigidity is critical for achieving the desired level of performance and accuracy․
Maintenance of Slide and Guide Systems
Factors to Consider When Selecting Slide and Guide Systems
Selecting the appropriate slide and guide system requires careful consideration of various factors to ensure optimal performance and longevity in the intended application․ Load capacity is paramount; the system must be capable of handling the maximum expected load without exceeding its rated limits, which can lead to premature failure or reduced accuracy․ Travel accuracy is another critical aspect, especially in applications demanding precise positioning․ Different types of linear guides offer varying levels of accuracy, so it’s essential to choose one that meets the specific requirements of the application․ Rigidity is also a key consideration, as it affects the system’s ability to resist deflection and maintain stability under load․ The environment in which the system will operate plays a significant role in material selection and sealing requirements․ Harsh environments with exposure to dust, moisture, or extreme temperatures may necessitate the use of corrosion-resistant materials and robust sealing to protect the internal components․ The required travel length and speed should also be taken into account, as some linear guides are better suited for long-stroke applications or high-speed operation․ Cost is always a factor, but it’s important to balance upfront expenses with long-term performance and reliability․ Finally, ease of installation and maintenance should be considered, as these factors can impact the overall cost of ownership․ By carefully evaluating these factors, engineers can select a slide and guide system that delivers the desired level of performance, reliability, and value․